Plano Foundation Repair is usually a big job and should only be done by qualified contractors. There are several warning signs to look out for including cracks in walls and uneven floors.
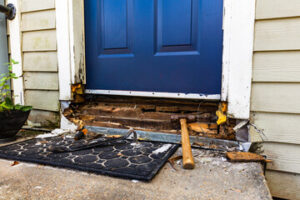
Recognizing these signs early and addressing them promptly can help to avoid further damage and keep your home stable. There are a few different methods for repairing foundation problems.
If your foundation has settled, heaved or shifted out of place, a support pier system can lift the foundation and restore it to its proper position. The type of pier used depends on several factors, including soil conditions and the type of building. To make the best decision, homeowners should consult with professionals who can assess and recommend the best solution for their needs.
The most common types of piers used for foundation repair are concrete and steel. Both are designed to transfer the load of a foundation from the ground underneath to more stable layers or bedrock. The piers are installed by digging small holes around the foundation, then using hydraulic machinery to drive steel or concrete segments into the earth. Once they reach a firm layer of soil, the piers will be capped with concrete to provide long-term stability and prevent future shifting.
Concrete piers are commonly used for commercial buildings, but they can also be applied to residential properties. They are typically affordable, versatile and offer good long-term durability. To enhance their load-bearing capacity, on-site crews can add reinforcing bars, or rebar, to the piers. The rebar will add more tensile strength, preventing cracks and excess shifting when the concrete settles.
Because concrete piers cannot penetrate as far into the ground as steel piers, they are not ideal for all applications. They are typically only driven down to a depth of about seven feet, which may not be enough to reach stable soils in some cases. However, they can be capped with steel to extend their life and improve their performance.
Steel piers are often preferred for projects in challenging soil conditions. Their screw-like design allows them to penetrate deeper into the ground, providing a secure anchor that can stand up to heavy loads. They are also much more cost-effective than concrete piers for most projects. However, it is important to note that steel piers require more maintenance, because they must be regularly inspected for signs of wear and tear. This may mean that they are not the best choice for many property owners.
Steel Piers
Steel piers are a great option for foundation repair because they can be driven farther down into the ground than concrete piers. This allows them to more effectively support and stabilize buildings on shifting soils. In addition, steel piers are more resistant to environmental wear than concrete, making them a long-term solution for your foundation.
The process of installing steel piers is similar to that of concrete piers, but the excavation required is usually smaller. First, the team must clear the site of the foundation problem. Once this is done, tarps are laid down to protect any landscaping or structures that may be affected by the process. Then, the crew digs a hole in the area surrounding the structure, using either hand tools (for small shops and homes) or larger variations of auger drills. A temporary bracket is then positioned along the structure’s foundation, and a hydraulic press is used to drive steel pipe segments vertically into the ground. The driving stops once many layers of pipes have reached a load bearing strata beneath the surface.
Once a sufficient number of piles are installed, hydraulic jacks can be used to lift the foundation and return it to its original position. The Field Technician carefully monitors the reaction of the structure as it is lifted to make sure that there is no strain placed on the new piers. Once the building has been brought back to its proper elevation, the piers are locked into place, and the hole is filled in.
Helical piers are another type of steel pier that is commonly used in the foundation repair process. The name “helical” refers to the plates welded onto the pier shaft that give it its strength. Like a steel interlocking pier, this type of pier is driven into the ground until it reaches bedrock or a suitable bearing stratum. Each helix is then interlocked with the previous one to create a continuous, reinforced support column that can withstand significant loads without shifting or sinking.
The installation process for helical piers is similar to that of other types of steel piers, but it typically takes less time and requires minimal excavation. The drilling process is also more accurate, and helixes are more easily inserted into soils that have high clay content. This makes helical piers ideal for situations that call for a quick and easy solution, such as for pre-fabricated structures or commercial buildings that experience serious foundation settlement problems.
Soil Stabilization Methods
The quality of soil underneath a foundation can significantly impact the stability and longevity of any structure built upon it. This is why effective soil stabilization methods are so vital for a successful construction project. Whether through chemical or mechanical means, these methods improve the engineering properties of the soil beneath structures, helping to prevent future damage from climate changes, moisture conditions and other factors.
The most popular soil stabilization techniques involve chemical additives, such as lime, cement or fly ash, which improve the strength and durability of the dirt. This makes them ideal for heavy construction projects, as they increase the load-bearing capacity of the soil and reduce permeability, making it more resistant to swelling and erosion. They are also less susceptible to mechanical stresses, ensuring that any structures constructed on them will be durable and safe to use.
Alternatively, there are mechanical methods for soil stabilization that involve physical techniques like grading or compaction. These processes make the dirt more dense by filling in voids, which helps to reduce movement and settle. This method is ideal for smaller projects that require stabilization without the addition of chemicals, and it can be used in environmentally sensitive areas where chemical additives are not allowed.
When it comes to preventing structural damage, soil stabilization is one of the best tools that any homeowner or construction company can have in their arsenal. Stabilizing the soil under a home or commercial building before construction starts can prevent costly foundation repairs later on down the road. It can also help to avoid issues such as cracks in the walls and floors, doors that won’t close properly and uneven surfaces.
For homeowners, Gridlock’s advanced soil injection treatments can permanently break the swell-shrink cycle of expansive clay soils, reducing the risk of structural damage to homes and businesses. These noninvasive, cost-friendly solutions are safe for children, pets and plants and can be applied to pre-build sites or existing homes. For example, Douglas Foundation Repair’s AGSS-ICS ionic clay soil stabilizing treatment requires less than a day to apply and begins working immediately. This nontoxic, no-dig solution is more effective than traditional excavation and construction methods, saving both time and money.
Repairing Cracks
Some cracks are harmless and will likely disappear on their own, while others signal serious structural issues that require professional intervention. Regardless of the severity, any crack should be addressed as quickly as possible to prevent further damage and protect your home’s stability. If the crack is due to shifting soil, you may need to consider underpinning or carbon fiber straps to reinforce the foundation. Alternatively, you could use helical wall anchors or wall plate anchors to stabilize the foundation of concrete slabs. If water is the problem, it could be a simple matter of cleaning gutters, redirecting downspouts, or adjusting the landscape to ensure that water drains away from the foundation.
Stair-step cracks in brick or block foundation walls are often caused by the natural movement of soil beneath the structure. If these cracks appear in load-bearing walls, it is essential to contact a foundation repair contractor for professional advice as these cracks can indicate a serious problem.
If your foundation cracks are cosmetic or a few inches wide, you can fill them with polyurethane or epoxy caulk. Using a caulking gun, force the material into the crack and along its entire length. This type of filler is flexible and will allow for expansion and contraction without affecting the structural integrity of the wall.
Once the crack has been filled, it’s important to apply a waterproof masonry sealer to prevent water from infiltrating the wall and further damaging your foundation. This step is especially important if your cracks are due to a drainage issue or changes in the moisture level of the soil.
To ensure that the masonry sealant sticks to the surface, it’s important to clean the cracked area and about two inches behind it. Scrub the area to remove any dirt, loose debris, or paint, and make sure you are down to bare concrete. Then, affix the application ports to the outside of the crack and carefully seal each port with epoxy. When the epoxy has cured, you can cut off the ports. It is a good idea to check the product’s guidelines for specific curing times and environmental conditions.